News
Overcoming the 5 Major Challenges in Human-Robot Collaboration
The landscape of industrial automation is rapidly evolving, with collaborative robots (cobots) leading the charge in revolutionizing production processes. As a trusted automation solutions provider, Air Hydro Power understands the growing need for efficient automation in the face of skilled labor shortages and increasing production demands.
The Current State of Human-Robot Collaboration
Modern collaborative robots have opened new possibilities in automation, particularly in scenarios where traditional automation seemed impossible. These cobots excel in their ability to work alongside humans, offering both flexibility and enhanced productivity. However, implementing effective human-robot collaboration (HRC) requires careful consideration of safety measures, especially when humans and robots share the same workspace.
Key Challenges in Human-Robot Collaboration
Based on industry experience and insights from SICK’s comprehensive research, here are the five major challenges facing HRC implementation:
1. Implementation Simplicity and Cost-Effectiveness
The ideal robot application should be quick to deploy and economically viable. Cobots have emerged as the perfect solution, offering:
- Rapid installation capabilities
- User-friendly programming interfaces
- Cost-effective implementation
- Built-in safety features for collaborative operations
2. Accessibility Without Barriers
Modern manufacturing demands flexible access to robotic workstations. Operators need the ability to:
- Monitor work progress
- Make immediate adjustments
- Perform quality checks
- Intervene when necessary All without triggering unnecessary safety stops or dealing with restrictive physical barriers.
3. Balancing Productivity with Safety
Finding the sweet spot between operational efficiency and risk reduction requires:
- Thorough risk assessment and engineering
- Minimal interference with productivity
- Cost-effective safety solutions that don’t compromise protection
- Strategic protective field placement
4. Workplace Ergonomics and Worker Acceptance
Traditional safety measures often rely on contact-based technologies, which can create uncertainty and discomfort among operators. The key is implementing contactless safety solutions that build trust and confidence in the collaborative workspace.
5. Economic Viability
The success of HRC implementation depends on:
- Efficient operation alongside safety measures
- Reasonable implementation costs
- Quick return on investment
- Minimal impact on productivity
A Revolutionary Solution: End-of-Arm-Safeguard (EOAS)
One groundbreaking solution to these challenges is SICK’s End-of-Arm-Safeguard (EOAS) technology, developed in partnership with Universal Robots. This innovative system:
- Creates a cone-shaped protective field around the tool and workpiece
- Moves with the robot, providing dynamic protection
- Enables higher operational speeds while maintaining safety
- Eliminates the need for extensive force and pressure measurements
- Builds operator trust through contactless protection
The Future of Human-Robot Collaboration
As automation continues to evolve, solutions like EOAS represent the future of safe and productive human-robot collaboration. These technologies enable manufacturers to implement collaborative applications more broadly, moving beyond niche uses to widespread adoption across various industries.
This blog post was inspired by insights from SICK’s comprehensive analysis of human-robot collaboration challenges. Read the original article here to learn more about SICK’s innovative EOAS technology.
For more information about implementing collaborative robots and safety solutions in your facility, contact Air Hydro Power’s automation experts today.
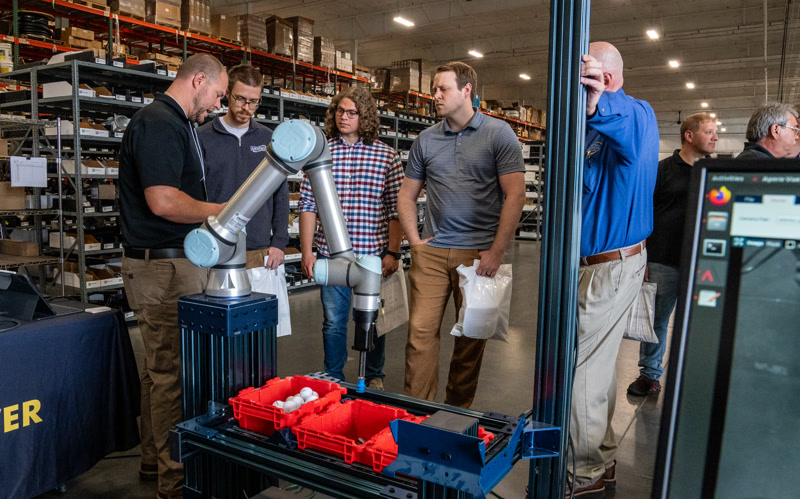